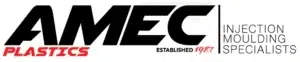
AMEC Plastics explains how, due to border closures, they implemented AspectPL completely remotely with the AspectPT team.
AMEC Plastics began trading in 1987 because a model plane hobbyist wanted to make his own model engine components. After purchasing its very first injection moulder, the Aeroplane Model Engine Company (AMEC) was started. Many years and iterations later, including making laundry powder scoops, caps and closures, AMEC Plastics is still running and thriving today.
Based in Queensland, AMEC Plastics still makes caps, closures and food packaging but have also diversified their product range. They now also make medical devices and electrical housings for companies like Siemens and Henkel as well as products for the Royal Australian Mint.
In 2021 AMEC decided it needed an MES (a digital manufacturing execution system). AMEC were running a manual manufacturing process with no automated scheduling. In fact, they didn’t even have a dedicated Production Planner. With the business growing and plans to move into larger premises they knew they had to invest in an MES to manage the production floor.
Recommended by a current user, the AspectPL MES was proposed. AMEC Plastics General Manager, Jy Lovett and the AMEC team had their first online meeting with Shayne Jones and Bob Dedekind from AspectPT in May 2021. By August, in just three months, AMEC Plastics was up and running with AspectPL managing their production operations.
To add a degree of difficulty, AspectPT is located in Auckland and AMEC Plastics are in Burleigh Heads. So due to border closures, the AMEC Plastics – AspectPL implementation was performed completely remotely. Initial online scoping meetings, implementation, go-live and training have all been conducted remotely. In fact, the AMEC Plastics and AspectPT teams have never even been in the same room, or even the same country!
Jy Lovett, General Manager of AMEC Plastics said: “The implementation went smoothly – it’s been a good process. The literature from AspectPT helped and the guys at AspectPT, especially Chris Rauch have been very generous with their time and really, really helpful.”
Now AMEC Plastics have employed a new Production Planner and, in a few months, they will move premises and take their factory from 12 to 17 lines. They want their operation to have the capabilities of a bigger business while retaining the flexibility of a smaller business.
They are looking forward to using AspectPL data more and more to improve production efficiency and plan to use the AspectPL Maintenance Module to help them manage production moulds.
“My feedback for AspectPT – everything has been fantastic – keep doing what you are doing.” Jy Lovett, General Manager, AMEC Plastics.